Primitive Skills; Making Steel From Iron Ore
Welcome to the website “primitiveskills.net“. If you’ve been following from previous posts, you’ll know I’m transitioning from the Stone Age to the Iron Age, especially during iron production, if you don’t know, you can join here.
In this article, I want to introduce you to the process of producing iron in a primitive way with the “primitive skills“. First I took a primitive ax and a bamboo basket into the hills where there were rocks called iron ore. This ore is distinguished by the naked eye, has many colors in a lump but is characterized by two colors: black and brown (dark brown, brown); kidney shaped, dense or porous like iron residue. This ore has an iron composition of 53% to 56%, hardness 1-4, density 3,4-4.0.
After some time of searching and digging, I have found quite a lot of ores. Because of the high content of iron inside, heavy ore, with the power of a normal adult, it can only yield about 35-50kg / per turn, so I have to divide several times to bring them back, After I brought them all to my house and put them in a neat pile.
Next I went to the forest to find a sufficient amount of firewood to allow the process to heat up, making the ore brittle. Choose firewood that is sufficiently dry, flammable, and it is important to add small pieces easily. After the vaccines arrived, I cut them into lengths of about 1m, and then cut them one by one into small pieces. If logs are large enough to be replenished, wooden chisels need to be separated. After hard work I managed to separate all the wood. Next I smashed the ore into small pieces, put it in a basket and 2 garbage containers. Now you can take a closer look at the ingredients in the iron ore that I smashed.
I arranged the sticks into 3 layers, in the bottom layer I left a space to allow oxygen to fit in so that the combustion went better, the strip of all the ore was smashed to the top of the last layer of firewood. then proceed to burn the wood. The purpose of burning this ore is to make it brittle to easily crush it and make it easier for the next step. After an afternoon of burning, the wood was completely burnt and the ore inside was red hot. Then leave it as it is, until the next morning when the coal and ore have cooled, we can see that the ore has turned a bit brighter and is especially brittle and easily broken. Next take a bamboo “sieve” and place a millet inside, using a wooden hammer to smash each ore into the smallest possible pieces of ore. Because the debris was so slow, I used the water-running mortar (Monjolo) to crush them. After working day and night, I finally crushed all of my ore.
Next I checked whether the air blower, furnace, wind system was open or not, and prepared equipment such as: wooden spade for ore burning stage, wooden hammer for salvaging iron or iron dam. After firing, the stones and other necessary lumps of wood. Examine through the main material of ore and the baskets of coal stored from the previous year. After everything was fine, I proceeded to cover the front hole of the kiln and removed the red coal from the stove through the mouth of the furnace inside the furnace, added a small batch of coal and blew it out with a wind pump. Blowing until the previous batch of coal burns red, proceed to the next batch. When I had enough coal underneath me, I put in small batches of ore into the furnace. Note, after adding a layer of ore to the furnace, a layer of coal must be added to avoid clogging inside the furnace; choking inside the furnace will result in an unburnt fire, as a small amount of oxygen will not melt the ore and the worst result will be the failure of the project. So the process of distributing the ore into the furnace is also very important.
The above stage is based on the metallurgical principle: When iron ore, coal is arranged in layers. The hot air blows from the bottom to meet coal (C) and burns carbon dioxide or carbon dioxide (CO2): C + O2 (temperature) -> CO2 (gas); continue to burn and form Carbon Monoxide: C + CO2 (temperature) -> 2CO; Thanks to the carbon monoxide reducing iron oxide: 3CO + Fe2O3 (high temperature) -> 3CO2 + 2Fe; MnO2 and SiO2 aggregates will be reduced to single substances; Limestone decomposes into CaO and oxidizes some impurities mixed with ores such as SiO2 to form slag. Slag should float slightly above and outside the furnace door: CaO + SiO2 (temperature) -> CaSiO3. Gas is generated in the furnace and is released at the top near the mouth of the furnace.
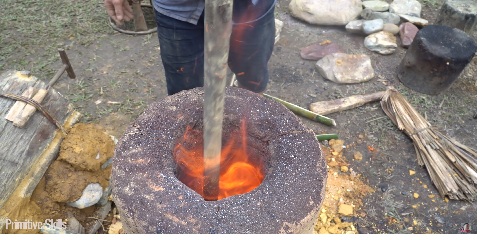
(ore processing)
After a hard-working day, a large portion of the ore was baked. By the time coal fills in the kiln, we stop adding ore. Check and remove the furnace to get iron from the furnace. At this point we see the amount of pure iron will be melted and clumped together into a lump, clinging around it is the iron residue. Use a wooden hammer to break each bit to remove iron residue. At this time, the iron we see there still contains quite a lot of iron shit, to complete it, please follow up in the next article. After obtaining an iron lump as shown in the video, we bring it to cool down with water, bring it to sharpen so that we can take a closer look at iron.
It was almost dark by now, after reviewing the rubble there was nothing more, I proceeded to clean up the condensed contents into the house and the hut to avoid rain.
Thank you for reading the article on “primitiveskills.net”
See you at the next article
Was directed to your series on bloomery iron smelting.
It would be very helpful to know where you are working, who YOU are – and your general background.
As someone who has experimented with North European ‘Migration Era’ (600 – 1000 ACE) I can see a couple of things that seriously effected your results :
– You appear to have added your ore in the ‘layer cake’ method (stacking furnace with layers of ore and charcoal, then burning down). It is far more successful to fill the whole furnace, keep it full, then add ore in handfuls with charcoal once the whole stack has ignited.
– You have not left much of a gap between the tuyere and the hard (clay) base of your furnace. The bloom is formed *below* the tuyere. You need to leave room!
– Your entry angle for the tuyere looks extremely flat (maybe about 5 degrees?) This causes the developing slag bowl to sit too high, and then quickly to drown your tuyere. An angle of between 15 and 25 degrees has proven most effective. (I use roughly 22 degrees myself)
– The clay tuyere? some description of that would be helpful to understanding.
Given your description of ore quality, those suggestions would have given you both a far more dense bloom – and much higher end yield of iron.